After we chatted last week about slate frames, tensioners, and the like, I thought I’d revisit the topic today after making adjustments and playing around further with slate frames all week.
Just like Bach and his well-tempered claviers (which I happen to be listening to as we speak), I say you can’t go wrong with a well-laced slate frame.
And that point is pretty much the upshot of this week’s toying about. But! There’s more to it than just that.
For those of you exploring framing options, slate frames and their tension is a topic worth pursuing a little more, think. There were some questions that rolled in last week – and some ongoing discussion back and forth with some readers on the topic of frame tension – so I thought I’d bring up the questions and some of the points that were discussed.
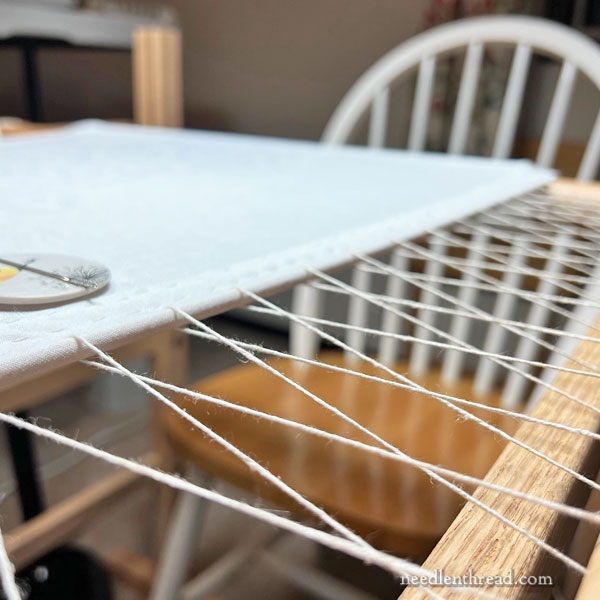
In the coming weeks and months, the slate frame is going to show up a bit more frequently here on the website. I have some work to do that will benefit from the excellent set-up that one can achieve with a slate frame, so I’m planning on using slate frames and similar for that work.
Last week, we talked about side tensioners that are made out of shock cord and clips, and whether or not they work well for tensioning. I liked the idea of using something other than lacing cord – which I always run out of right when I need it most – for lacing frames. I like the idea of something reusable and reliable.
And the tensioners do work. What I’ve found is that they need adjustability, though, and not just in the spacing of where you can attach the hooks. They need adjustability in minute degrees. And you need to be able to tighten them or loosen them as needed.
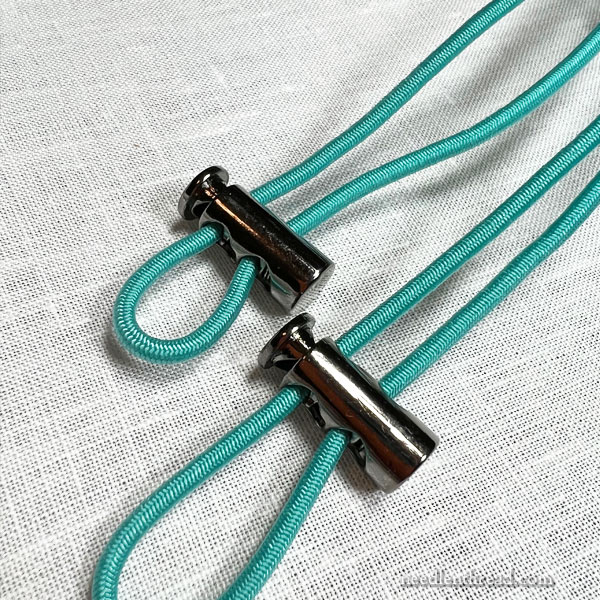
So to that end, I made some tensioners with these slide clip thingies and tried them out.
They do work, but…! They work better, in my opinion, on small frames and small projects. In fact, they work very comfortably and easily on smaller frames.
I like them pretty well!
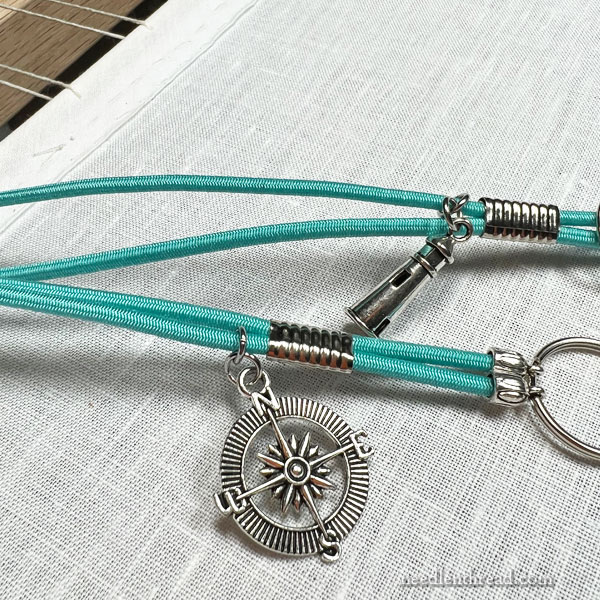
Hey! And the fact that I could bling them well up didn’t hurt things, either.
(What is it about decorating accessories and tools? Hmmm. I might have a little obsessive problem with that.)
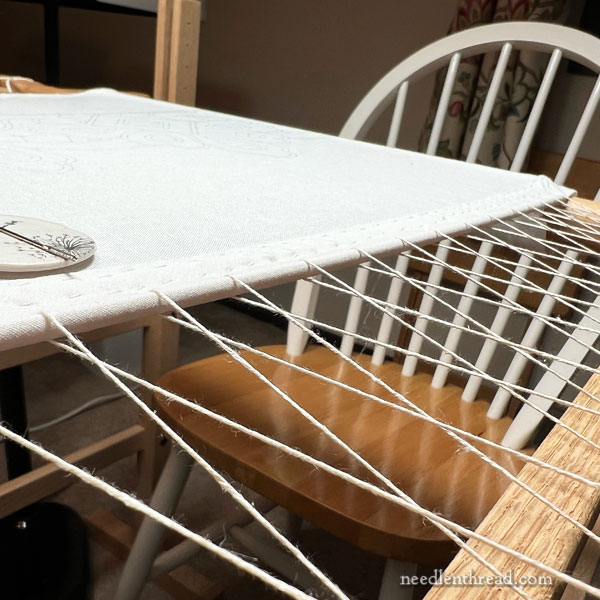
But for a large project, on a large slate frame, darn it. There’s no getting around it! Nothing beats a good lacing job!
Remember, the things I’m framing are Big Projects – there’s a whole lot of extra linen rolled on the rollers on the frame (which tends to reduce the amount of vertical tension you can achieve), and so that side tension, to me, is pretty important. And wow. You get fabulous side tension when you lace a slate frame correctly.
I mentioned that I use linen string to lace my slate frames. Linen is a super strong thread. It’s never caused me a problem. But I am not a stickler who says “It must be linen string, or naught at all.” If there’s a decent string or cord out there that will give me good tension with very little stretch, I’m all for it!
Some of you who weave recommended some string that would work well for lacing, so I tracked down two different types to try. One is linen. One is a cotton-poly blend that resists stretching and is used for warping frames for weaving carpets and such.
So thanks for those recommendations! Down the road, I’ll share the results for those who are interested.
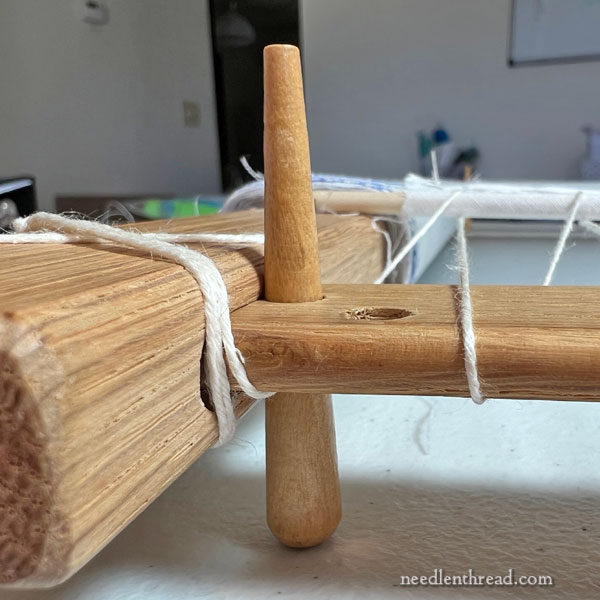
Another topic that came up after last week’s article was the question of wooden pegs. I happened to mention that I prefer steel cotter pins.
(Normally, pegs go down into the side slats on the frame, narrow end first – not like in the photo above. Just wait a second, and I’ll explain!)
When I use pegs shaped like the one in the photo above, I find that the pegs are always wanting to peg out if they’re put in from the top down.
If the frame is propped on the edge of a table or sitting flat on a table so that the pegs – which are longer than the frame is deep – are what come in contact with the table, then the frame goes down and the pegs push up and out.
Drives. Me. Nuts.
There are ways to get around it, I suppose. You can put some kind of elastic or rubber something-or-other on your pegs to help hold them in.
Or you can do what I do and put the pegs in from the back (upside-down, essentially). The obvious problem with this approach is that, if you are moving your frame around and your work is face up, you risk the pegs falling out. But the upside-down peg configuration works better for me the majority of the time. If I have to use a frame with this shape of wooden peg, they go into the frame upside down, as shown in the photo above.
There are other shapes of wooden pegs, too. I have a set that have a little ledge on them, that locks the peg into position and holds it there, somewhat. If there’s not a lot of pressure on the peg, then they stay in place quite well. Alas, I only have three of the four pegs in that set.
So, anyway, I like cotter pins better. The holes on the side slats are a lot smaller, so that you have smaller, more precise increments for stretching, and the cotter pins have better staying power in their little holes.
And a Massive Slate Frame
I ended up ordering a slate frame from Ecclesiastical Sewing to get ready for some upcoming work. The frame I ordered is massive compared to any of my other frames. The tape on the rollers is, I think, 44″ – so the frame itself is 52″ wide. Whooooohooooo! That’s Huge.
It’s a gloriously well made frame. The side arms fit perfectly, the feel of the wood is so nice. I’m so happy with it. Yes, it’s a Big Investment, but it will last forever. And I have some Big Plans for it.
So, that’s a little tie-up on the slate frame subject and tensioning. I will most likely use the tensioners I made for smaller projects on smaller frames, so they were certainly not a wasted exploration. In fact, I’m making more of them! We may very well visit that whole topic again some day, since some smaller frames will be figuring into some of the upcoming work here.
On big frames, though, lesson learned. Lace it! You’ll love it.
Looking for More Information?
If you’re looking for more information on slate frames, I’ve written about them off and on. You can find many of the articles on slate frames – including reviews of various frames available – listed here.
I have a question about using a slate frame. I’ve tried one in the past and found that when the edges of the fabric have been hemmed, when it is rolled around the rods, it might be tight on the rollers at the edges, but saggy in the middle of the roller where there isn’t as much bulk. How do you adjust for that?
Thanks, and have a fruitful Lent,
Monique
Hmmmm. I’ve never had a slate frame with anything saggy in the middle. If you’ve got the sides tensioned horizontally and the rollers (top / bottom) tensioned vertically, I’m not sure how there can be sag. I’ve worked on slate frames that are 40″ wide and larger without having this problem. It’s pretty much all about tensioning the sides and rollers correctly.
When you say you use linen “string” is this bookbinders linen cord? What thickness do you use and where do you source it?
Thanks.
I don’t have any bookbinder’s linen cord to compare it to, so I’m not sure. The stuff I have is about as thick as a #3 perle cotton, not under tension (perle cotton gets a lot thinner when you pull on it). It is on a cardboard tube, and unfortunately, I can’t find the information on it. BUT – I am looking for it, and when I find it, I will probably re-visit this topic, since I have a few different types of string for lacing that I can compare for everyone.
Do slate frames have any feature which prevents them warping the way a scroll frame does? Maybe I’m just using it wrong, but I find it is easy for a corner of the frame to move out of the plane where I think I’ve got it all nice and perpendicular, causing the fabric to get pulled at an angle rather than straight.
I’m a bit confused about string and thread, I think. I think of string as thicker stuff (even thin string) and I’ve only seen linen thread for sale (and that only in smallish quantities). Not that I have a frame to lace, so it’s a real confusion but a merely hypothetical problem.
Well, when it’s under tension, the sides are pulled in and up against the cut in the rollers, and then, you wrap your excess in an X configuration around the intersection of slats and rollers, and it secures them so they don’t go off kilter easily.
I probably use the terms string and thread interchangeably with this kind of stuff. But the linen thread I use is a heavy linen thread – it’s sold as linen thread, I think. It’s just a very heavy linen thread. But you might call it string, if it’s too heavy for thread in your mind.
Hi Mary,
Would you let us know what size linen string/thread you are using? A link to the one you use would also be nice.
Hi, Oriole – I don’t have the info on that! I’ve been looking. It’s linen that I have on a cardboard spool, but I’ve lost all the info on it. I’ll keep looking…