I had a terrific time tackling my Needlework To-Do List this weekend!
Let’s see… there were twelve things on it. I managed two.
On the bright side, one of the Managed Things was the set-up for a project that’s been simmering on the back burner for a while – namely, the frame for this salvaged piece of figure embroidery.
I’ll be working this salvage job in two major steps. The first step will be the goldwork frame. And to get to the point of actually doing the goldwork, I had to set up a slate frame with a piece of fine linen as the ground fabric.
I went about setting up the ground fabric and frame a little differently, but that’s the nice thing about embroidery. There’s no set rule that says you must do This or That (in this case, setting up the slate frame) one way or another. As long as the system works, then you’re good!
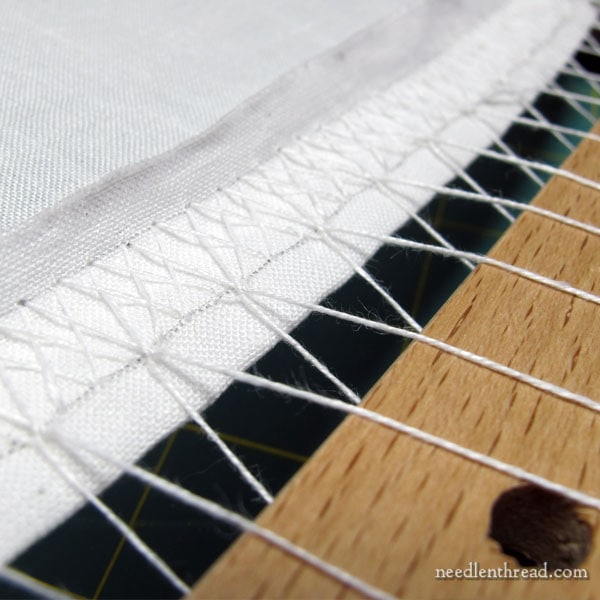
For those just getting into embroidery, if you’re not familiar with what a slate frame is, I’ve written about them several times here on Needle ‘n Thread. This is a list of articles about slate frames, in case you want to pursue the topic further.
There are different versions of slate frames, but the most common version is this type shown in this article. There’s also this type of slate frame, that handles the connection of the fabric on the rollers (the top and bottom parts of the frame) differently.
I’ve also written about how to dress a slate frame, but over the years, my process has changed to suit my project and the tools and materials I have on hand. The concept is still the same – you attach the fabric to the top rollers of the frame and you lace the sides of the fabric onto the side slats, so that you can tension the fabric from the sides.
Not Just Any String
If you’ve used a slate frame or considered using one and done a bit of research on them, you’ve probably seen frames set up with heavy string or twine as the lacing thread, laced through strips of heavy fabric attached to the edge of ground fabric by way of large upholstery needles.
And that’s all well and fine – it works! But it’s not the only way to go about setting up a slate frame.
One day, I was watching a French program on Luneville embroidery (tambour embroidery) filmed at a professional atelier in France, and I noticed three things about the side lacing on the frames:
1. The string was not heavy string at all. It was, in fact, a relatively light thread.
2. There was no reinforcing fabric on the sides of the ground fabric.
3. The lacing string didn’t pass through the fabric. Instead, it wrapped around sets of T-pins running down the sides of the ground fabric.
And that’s when it occurred to me that it doesn’t really matter how you set up a slate frame, as long as the set up does what it’s supposed to do: perfectly tension the fabric top to bottom and side to side.
Since then, I’ve slapped together slate frames in all kinds of ways.
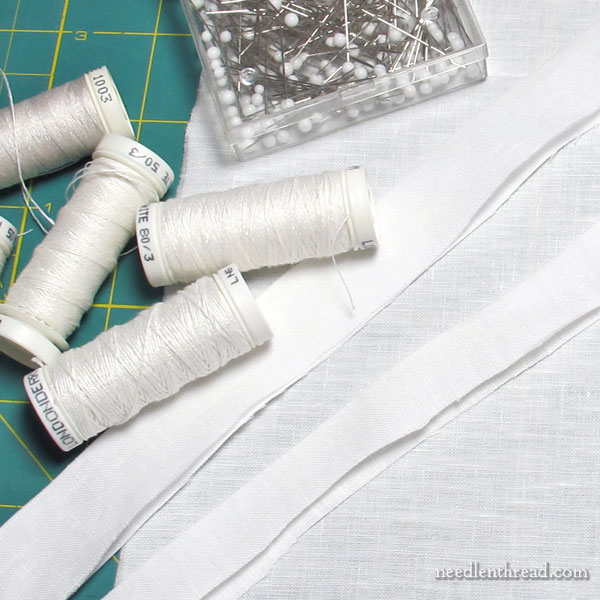
But one thing I’ve done consistently is switch from heavy string to linen thread for lacing the sides of the frames.
Why? Two reasons:
1. Linen thread is extraordinarily strong and it doesn’t stretch.
2. Linen thread can be handled with a regular crewel needle and it passes easily in and out of the fabric that’s being laced onto the frame. It’s finer and a lot less bulky compared to string, and it’s very easy to handle.
For the project I’m setting up right now, I’m using size 30/3 Londonderry linen thread for the lacing. I used a size 50/3 for other sewing involved, including attaching the fabric to the top and bottom rollers and sewing some reinforcing strips of fabric to the sides.
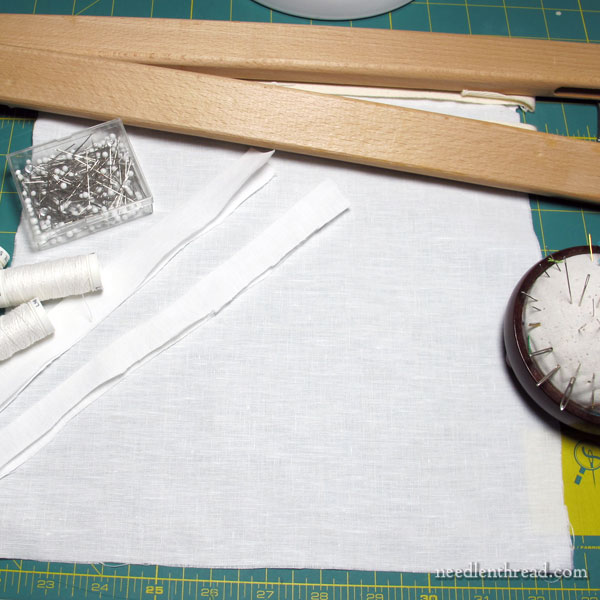
To set up this particular project, then, I used the following supplies:
- A slate frame
- Pins
- My ground fabric (in this case, a somewhat fine linen)
- Two leftover strips from the sides of my ground fabric, folded in half
- Linen thread sizes 50/3 and 30/3 (I use Londonderry linen because it’s consistently good linen thread available in a variety of weights)
- Crewel needles, #3 and #5
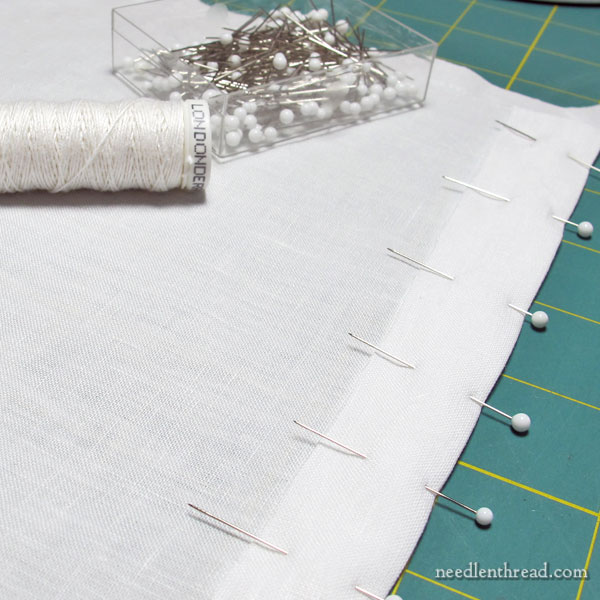
Because I’m using a very fine linen as the ground fabric for this piece (I’ll explain why later, when I start the goldwork), I reinforced the sides of the linen.
To do this, I just used two leftover strips of the same linen. I folded them in half and fit them over the sides of the ground fabric and pinned them in place.
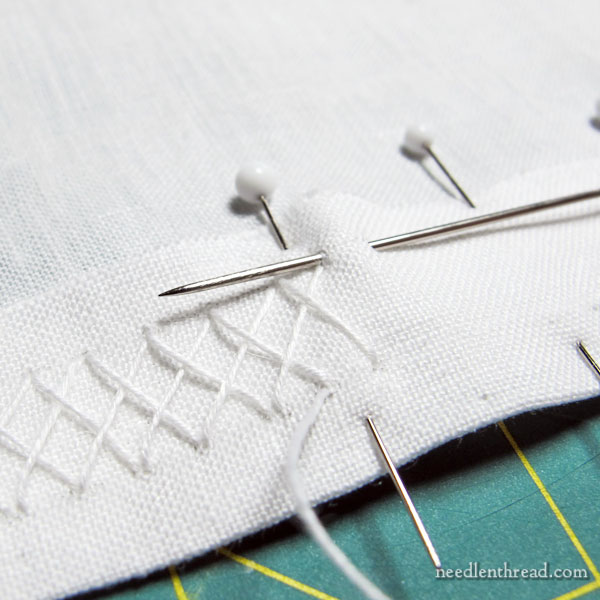
Then, using the 50/3 Londonderry linen thread, I worked a herringbone stitch over the folded extra strip that encased the side of the ground fabric.
I like this part of the process. And I probably overdo it a bit. The herringbone doesn’t necessarily need to be that close together, but hey – it’s not going to hurt it!
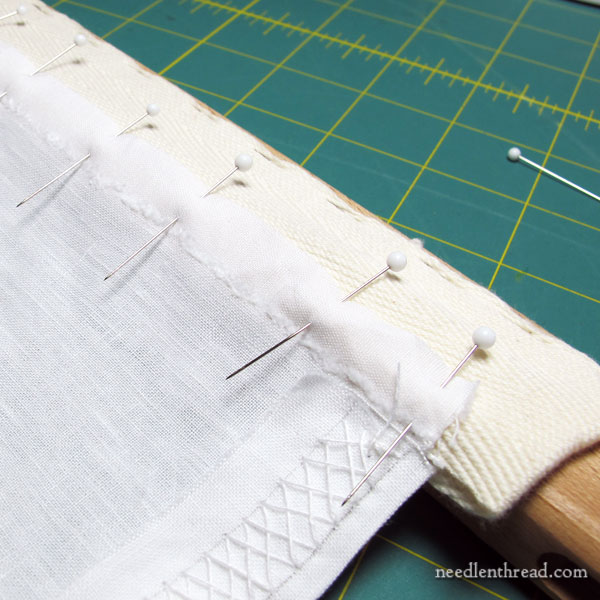
With the reinforcing strips sewn to the side, I pinned the top and bottom of the fabric to the rollers and herringbone-stitched them onto the twill strips using the same linen thread.
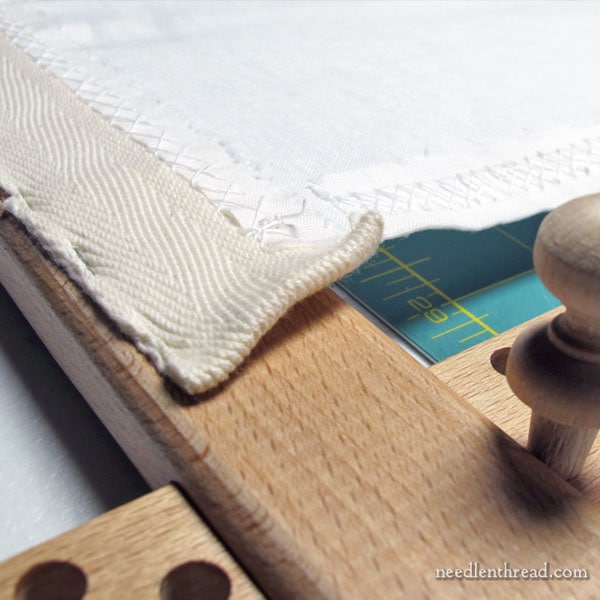
This might all sound like tedious work, but I find it engrossing and kind of meditative, once I get into it.
I always view the set up of a project as a Huge Hurdle to overcome, until I actually get into the whole process of setting up. And then I really enjoy it! The trick, I suppose, is just to get myself to start!
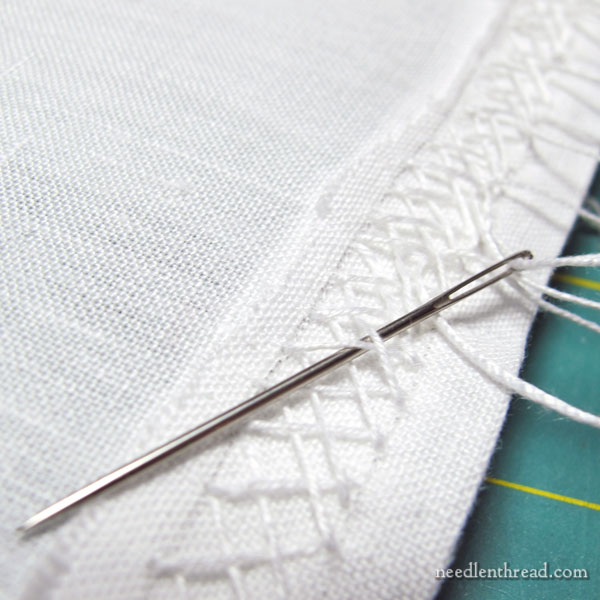
Instead of lacing through the reinforcing fabric strips on the sides, I just laced through the herringbone stitching.
I recently saw pictures of a huge frame set up with the lacing thread passing not through the fabric, but rather through herringbone stitching on the side of the fabric. It was a much neater job than this, and the method was slightly different. It worked magnificently on the huge frame!
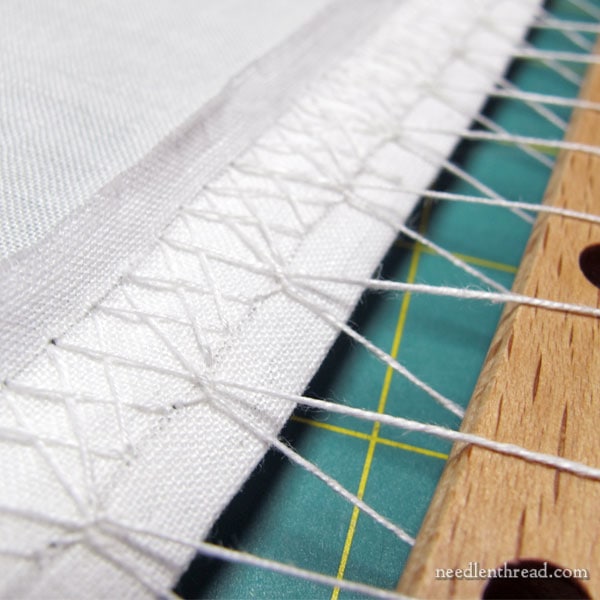
So, when I started lacing the sides of this, I figured why not? No need to pass through the fabric – just lace under the herringbone.
And it worked great.
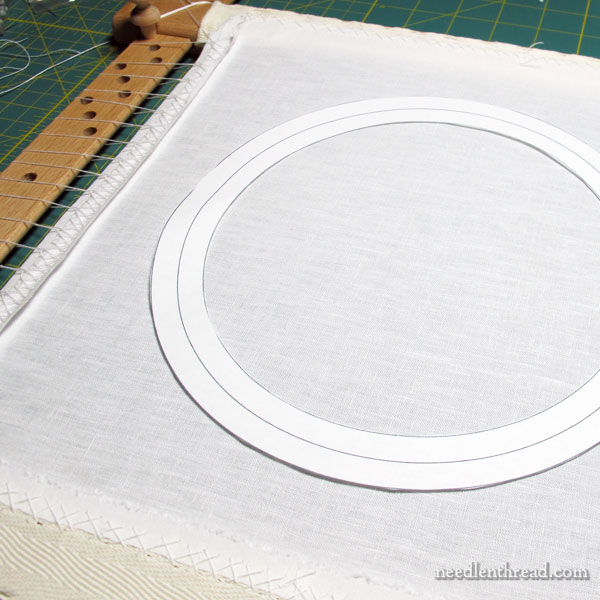
So, the slate frame is all ready to go!
The circle of paper you see in the middle represents the size of the goldwork frame I’ll be working. It’s just a simple, round 8″ frame.
Today, I’ll be tacking the wool felt onto the linen, and then I can start stitching the gold!
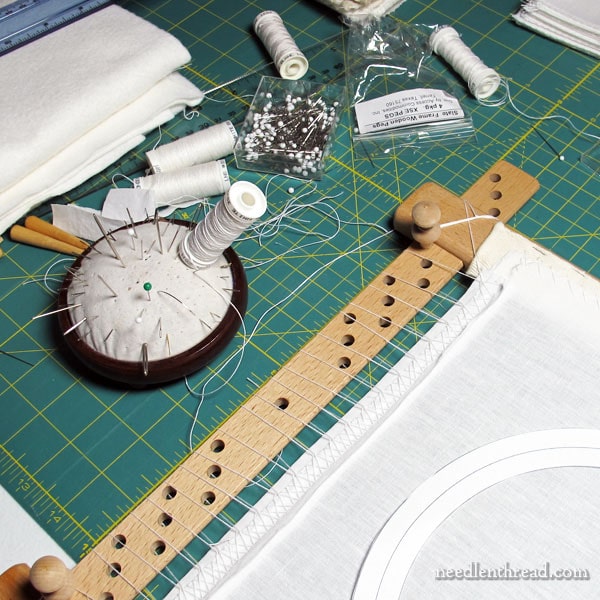
Of course, what started out as a rather neat, methodical-looking workspace ended up being a jolly mess at the end, clearly betraying me and my methods as anything but neat and methodical…
I’ll keep you posted on the progress!
If you want more yardage than the (very nice) Londonderry spools, a good source of linen thread appropriate for lacing is ” line” linen sold for weaving. It comes in many weights and is sold on large cones. I’ve been using one (about 1000 yard) cone for lifelines and lacing for several years!
Sources include the Yarn Barn of Kansas (in Lawrence) and Halcyon Yarns in Bath, Maine (both of which I’m a customer of, no other affiliation).
I, too, find set up to be one of those things that I dread in anticipation but rather enjoy in retrospect. I’m looking forward to seeing the goldwork. Having just done my very first tiny dabble with faux gold Kreinik braid, I REALLY want to try the real thing…….
Ah, good to know! Thanks, Karla – I pass through Lawrence now and then, so I might stop in some day!
The Yarn Barn is on Mass St. in the 900 block, parking in the city garage behind the shop across the alley (2 hrs free in the basement). Across the street from Sarah’s Fabrics.
Those two shops are my ‘not really local but on the way home from the KC office’ yarn and fabric shops. Now if there was only a local (ish) needlework store. I miss Sunflower Seed and the shop in Wakarusa.
Hi, Karla – I’ve been to Yarn Barn, but really only for wool roving and yarn gifts for my sister and niece who knit. I didn’t think to look there for linen thread, which I will do the next time I’m out that way. Every time I go in there, I’m tempted to take up weaving. I mean, Big Loom weaving. The looms are fantastic! And yes, I love Sarah’s. They’ve got a terrific selection of fabrics. I especially love their silks and garment fabric section in the back. I could spend a lot of time and money there. :-/ But… admittedly…Brits and Au Marche are my two favorite shops on Mass St. They’re just fun. I never went to the shop in Wakarusa – I didn’t know there was one. Have you been to Yak ‘n Yarn in Topeka? They have a very limited amount of very basic embroidery supplies, but a fairly wide selection of yarns if you’re into knitting, etc. They do have a fairly wide group of needlework-experienced folks who frequent the shop, from what I understand, and they can even arrange lessons in interesting techniques, like bobbin lace, for example. I’ve heard there’s a “new” needlework shop in KC – I think in the Overland Park area – that kind of took the place of Two the Point, which closed years ago. This new place probably opened two years or so ago? I haven’t been there, and I’m not even sure of the name. But it might be worth looking up, if you go into the KC area frequently.
Hi Mary,
I would like to understand how we can use T-pins to wrap the tread around… I don’t “see it”. Did you ever tried it?
Thank you very much for your blog and have a good summer!
Marie-Josee Robichaud
Well, let’s see if I can explain. Running down the side of the fabric, parallel to the edge, the T pins are inserted in the fabric in pairs so that each one is scooping up a little of the side fabric, and each two in a pair are parallel to each other and arranged head to toe. This creates a two-headed device of sorts to wrap the lacing thread around.
Oops, and no, I haven’t tried it. I might!
Dear Mary
So many to Dos on your list but at least you have made a start. A very neat lacing job it must have taken some time to set up but now you are ready to go, the londonderry linen thread seems to be very strong especially has it holds the fabric and the frame together. I look forward to your progress on this project and thanks for sharing with us how to set up a slate frame and for the photos, you don’t look that untidy you ought to see my desk.
Regards Anita Simmance
That is such a good idea with the side lacing. Can you still tighten it as needed? I also saw a large slate frame set up using pins and wide cotton twill tape. I tried it on a cross stitch piece I was doing on a scroll frame and it was wonderful not to have sagging sides. The pins were hidden by the tape.
The biggest problem with this was as I scrolled the fabric I had to undo the pinned sides and then redo them, of course this wouldn’t be a problem on a slate frame that fit the whole project.
I always use either the kind of linen thread sold at weaving suppliers (kind of expensive but tough) or perle cotton (cheap and cheerful) I find the cottton more practical for pieces used for demos at reenactments, even though it’s not as authentic, because use outdoors means they tend to get damp, and linen does stretch quite a bit when it’s damp. I think string would drive me nuts, I hate having to force a needle through anything. the herringbone is rather elegant, although it does look time consuming, I’ll be interested to hear what you think of it’s durability once the piece is done
Dear Mary,
Thank you for such an interesting article. This looks like a very good method of setting up a frame.
I’ve been looking for 30/3 and 50/3 equivalents here in the UK. The only Londonderry I found was 18/3. Could you help me relate these others to the 30/3 or 50/3?
One is https://airedaleyarns.co.uk/index.php/yarns-
fibres-for/weaving/white-pure-linen-
undyed.html#accordion which lists 10/4nm (??), 20 Wraps Per Inch (WPI), 410m for 200g.
The other http://www.kurzke.co.uk/supplies/ goes to https://www.etsy.com/uk/listing/223624335/linen-thread-fil-au-chinois-fil-de-lin
“The number 8 has a diameter of approx. 0.8mm, No.
12 a diameter of approx. 0.65mm, and the No. 16
thread is about 0.55mm thick. ”
Can you help with identifying these? I have scoured around without success for relating this information.
Sincere thanks for your help –
Regards,
Helen
Hi, Helen – It would be really difficult for me to compare threads without seeing them in person and handling them. Of course, there’s the terminology that seems to govern the whole making of threads, but weight and thickness are often dependent on the original matter used to make the thread. To get the feel for 20 WPI, for example, and 410 meters in 200 grams, I’d still have to see and handle the thread to be able to make any relative comparisons to another thread.
If you’re looking for a thread to set up your slate frame in the same manner I did here, you’ll want a finer linen thread for the sewing part of it, and a heavier thread for the lacing part of it. The 18/3 in Londonderry is good for lacing. But it’s fine enough that you could actually use it for the sewing part, too – it would be a little heavier, true, but it would still work. It’s a good, sturdy linen thread.