To conclude this short series of posts on transferring embroidery designs to fabric, here (in one place) are my favorite methods of design transfer.
Again (I keep making this point – covering my “six,” as my dad would say!), I am not saying these are the Only Ways to transfer embroidery designs. But these are methods that have been safe and reliable for me, that I’ve used and have confidence in. For those who are looking for alternate ways to transfer embroidery designs, these may help you. If you already have a method and it works for you, then that’s great. I’m not dismissing all other methods. As is always the case on Needle ‘n Thread, I’m just offering what works for me, and how I do things, in case it may help someone else out there.
Note: always test your transfer method ahead of time on any major project, before you start marking up an expensive piece of ground fabric.
To determine what type of method to use, I always think in terms of the end product. Is the project meant to be washed? After I finish stitching it, can it be washed? If so, I proceed in one direction. If not, I proceed in another.
Embroidery that Can Be Washed
If I’m working on a project that can and will be washed after stitching – say, whitework on linen, regular cotton floss on cotton fabric or on linen, even wool on linen – then these are the methods I use for transferring the design.
Light, easily see-through fabric: After my fabric is washed (pre-shrunk) and cut and the edges are neatened, I spray starch the fabric and iron it. I like Niagara spray starch in the pump bottle rather than aerosol cans, personally, but I doubt the kind used really matters.
Then, using a sharpened HB pencil, I trace the design using a light box or a piece of plexiglass with utility lights underneath it, depending on the size of the project.
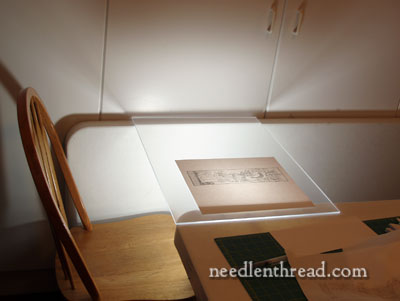
If I’m working on a fabric with a really smooth hand (it isn’t a bumpy fabric at all), I’ll sometimes use a mechanical pencil, but practically speaking, a mechanical pencil can be more difficult to trace with on fabric. It tends to catch. A regular pencil that’s been sharpened and that you hold at an angle, so that you’re “pulling” the pencil tip rather than pushing on it, works better for me. I don’t “sketch” with the pencil. I try to draw in longer, smooth, continuous strokes. Sketching tends to built up the marking or to make the line less precise (somewhat “hairy”).
This method above is fairly universal – anyone with a pencil and a sunny window can do it. Just tape the pattern to the window and tape your fabric over the pattern.
Dark or heavy fabrics: For transferring a design onto darker fabric (this is anything from a natural colored linen, for example, to black) or a heavier fabric where tracing is out of the question, I prepare the fabric as above, and then I use prick and pounce, with a light grey / white powder, made from a mixture of charcoal and talc.
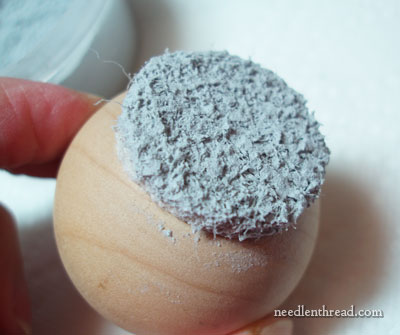
You can see how this method works by reading this tutorial on prick and pounce. With a dark fabric, I’ll use a lighter ceramic lead pencil to connect the dots, or a white tailor’s chalk pencil, depending on the type of stitching I’m going to do. The ceramic lead pencils are not as easy to smudge off as tailor’s chalk, and in fact, they are not always easy to get off altogether. So when drawing with them, I try to be as precise as possible.
Embroidery that Will Not Be Washed
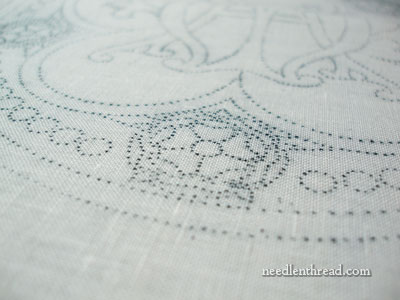
For embroidery projects that will not and cannot be washed – goldwork / silk projects, projects worked on silks, velvets, and so forth – I use one method to get the design onto the fabric (prick and pounce)…
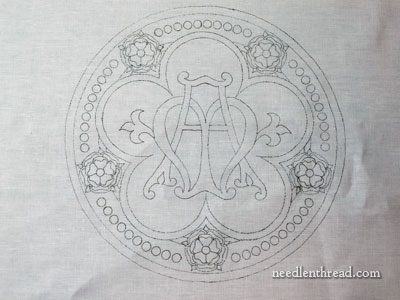
… and then I use either a micron art pen to connect the dots (like I did with the Medallion project)…
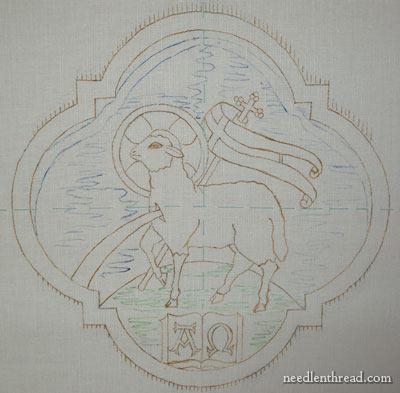
… or a very fine paintbrush and watercolor paint (like I did with the Agnus Dei project).
Other Reliable Methods of Design Transfer
Other reliable methods of transfer that I’ve used and that worked, and that, in certain circumstances, I would use again:
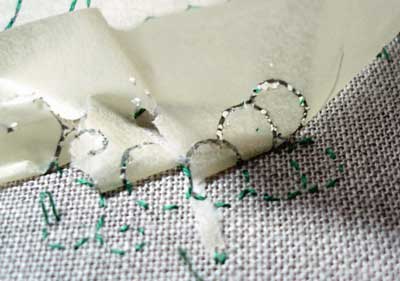
Tracing paper and tiny stitches – This is an accurate but time consuming way to transfer a design – but once it is finished, it really is worry-free.
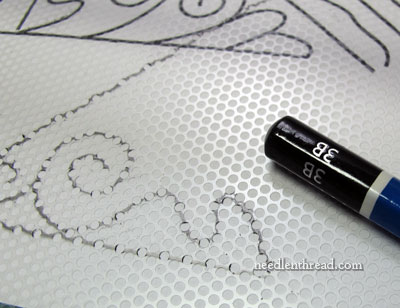
This Clover Transfer Mesh that started the whole discussion this week. For bold designs without much detail, this stuff works fine for getting a pattern onto fabric. I’d use it with a pencil when it comes to getting the lines onto the fabric, or with a ceramic pencil or tailor’s chalk pencil.
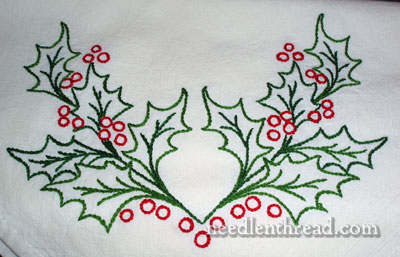
Water Soluble Stabilizer, Transfer-Eze, and the like – Understanding that there are different levels of embroidery projects done for different reasons, I have used these products and would use them again for certain types of stitching. Cotton on cotton, flour sack towels, children’s blankets and the like come to mind. I would not use these with silk, wools, on good linen, silk, or other fine ground fabrics – obviously, on anything that can’t be washed or that I’m putting a lot of money and time into. But for those quick projects for fun, with cotton floss on cotton fabric, they’re fine.
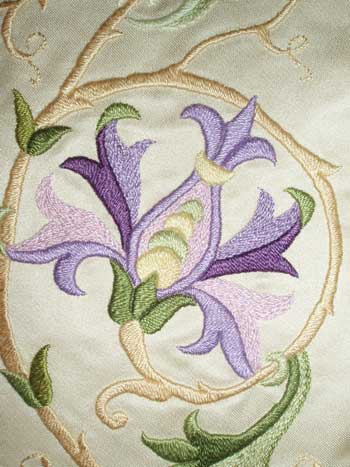
Wax-free Carbon Transfer Paper (like Saral) – I’ve used this successfully on light gold-colored silk, using the white carbon, and achieved a very clear design line that was visible while stitching and that lasted through a very long project. Because it was white on light gold fabric, any “visible” design lines not covered by stitching were, in fact, invisible. It’s not my favorite method, but I would actually use it again in the same circumstances, using the white on a lighter colored silk ground fabric. I’ve also used the blue paper successfully with whitework, but it requires really covering the design lines. The design lines don’t come out easily. I’ve heard disaster stories about the red, but have never used it myself.
Undoubtedly, I’ll still play with different types of design transfer. I’m game to try anything! But I can pretty much bet I’ll always come back to the first two methods at the beginning of this article – tracing and prick and pounce.
Now, onwards and upwards! Some stitching progress next week, among other things…
Enjoy your weekend!
It’s interesting seeing all these ideas in one place – it’s something I’ve struggled with since I started playing around with embroidery because I’ve always been afraid of those wash or fade-away marker pens. (I’ve been quilting for years and don’t use them there either, though they’re very popular.) But I couldn’t really decide what would be the best way to go about transfering designs. I’ve largely gone with the window-as-lightbox + pencil or micron pen method (because I didn’t want to buy prick and pounce or other supplies if embroidery didn’t turn out to be something I’d enjoy doing). So far it’s worked out for me, though I do find working with a lightbox/window to be hard on the eyes & arms.
I find prick and pounce the most reliable of the methods. I am terrible, and I mean terrible with the window method. I try to use a charcoal pencil with prick and pounce but I find that if I move the design too much the line disappears, so I am going to try the sepia watercolor next. It’s also a bit messy as it leaves a grey residue on the fabric, but since I wash all of my crewel wool work (with shampoo and very gently) and then I stretch them and set them (which also involves water), it isn’t that much of a problem.
Mary, your use of watercolour paint made me think about those watercolour pencils you see in the art stores… I wonder if they would be a good way to combine the pencil and watercolour paint methods? Thanks so much for this series – I am still battling to find the most comfortable method for myself!
I’ve tried them, Jeanine – they don’t always remove all the way, when you wash them, and it is difficult to get a dark enough line on linen to see well. They also rub out, if you are working in a hoop and holding the fabric, which was my biggest problem with them, as I was working on a Schwalm tablecloth in a hoop. By the time I finished one section, the other sections had to be re-transferred. MC
Thanks Mary – good to know!
Dear Mary
Thanks for your article on transferring methods. There’s so many ways of transferring a design but I like the prick and pounce method as it’s very accurate, I have just bought a light box and I will look forward to trying this method. As you say it’s essential to test various methods before transferring a design.
Thanks Mary very informative
Regards Anita Simmance
Thank you for allthese wonderful transfer methods.
I remember whenI was small (in France) my aunt used to have a little roulette wheel that pricked holes in the paper… Do you know if they still make those?
I’ve seen little wheels like that near the chalk pencils and in the paper crafts section at Hobby Lobby.
Thank you Katherine. I will go look! 🙂
They are a sewing item too. We used to use them for transferring dressmaking patterns. I think they should still be found in dress fabric shops.
G’day Mary.
Wonderful to have this all together. Thank you for your special efforts.
Cheers, Kath.
I used the wax paper method for a project where I had a very simple design/outline (a big gear). But instead of just doing tiny guide stitches, I embroidered the whole design over the wax paper. It worked very well.
Hello, Eve
Would you consider sharing a picture of the gear you embroidered?
I have a picture of an engine I want to do.
Thanks, surgery4
Unfortunately, while everything worked well from a technical standpoint, the project it was for ended up in disaster so I no longer have it. If you’re looking for an image to transfer, you can image search for vector art gears or due to the steampunk trend, someone may have already designed a nice pattern.
For those (like me) without a light box, my husband improvised a workable solution. Get a big, clear Sterilite plastic bin (like this one http://www.sterilite.com/SelectProduct.html?id=587&ProductCategory=179§ion=1) and a desk lamp with a goose neck. Put the desk lamp on a solid surface and point the light upward. Place the box upside down over the light. Now trace your design on the bottom flat surface of the box.
I also use a plastic storage box but mine is only about 4″ tall from the office supply store and I use a portable fluorescent light that runs on batteries for my light source. When I’m done the light, pencil & sharpner go in the storage box ready for the next time.
This is so helpful! I have a question about adding lettering to a piece that I have never found an answer to. I have several patterns with beautiful fonts but I know there must good way to create wording with these patterns and transfer them onto fabric without just eyeballing it. Thanks!
I just had a disaster happen. I used a very fine light brown pigma pen to mark an embroidery design. After finishing, I took it to the ironing board and gave it a quick shot of spray starch. Instantly the pigma ink ran as a shadow around the embroidery, but only where the spray starch touched it. Now I have no idea what to do. Do you have any suggestions. I have searched the Internet for a solution, but I haven’t found anything that seems safe. I could just cry!
Hi, Shawna – if you used cotton thread (like DMC – not over dyed, though) then you may as well try washing it by hand in lukewarm to cool soapy water. Use Ivory, or some simple detergent like that. I cant guarantee the results, but at this point, it probabl won’t hurt to try.
When using pigma pens, I generally avoid colors aside from sepia or black, and the only thing I apply to the cloth afterwards is a light mist of plain water. To finish (or “iron”) embroidery, try damp stretching, instead of ironing. Another thing (before the fact) to do is iron your fabric with a hot iron after drawing the initial transfer, face down on the ironing board. This can help set the pigma ink.
Hopefully, a gentle hand wash will take out the shadow. Let me know how it turns out…
Hi! Thank you for all the work you do that helps to educate and encourage us. As a new stitcher, I find you to be invaluable! Thank you (again). I have a quick question…what do you think of using an ink jet printer to transfer designs to fabric? Thanks again. I’ve been so encouraged and helped by your blog!
I’ve written about that here on the website – some folks do it. I love the idea of being able to feed fabric through a printer and come out with a perfectly flawless transferred design. But in my experiences with inkjet punters on fabric (I’ve tried a few different approaches with them), it works better with a flatbed printer (which increases the cost of the printer), and the prints don’t always come out clean. I think the more expensive flatbeds that are used for thicker materials would be best, but then you’re moving out of the realm of a home printer’s cost and into the realm of much more expensive printers, for something that is still somewhat risky for the printer.